Consumers lead the change - regulators trail behind
The speed of market changes brought about by consumer sentiment is increasingly rapid.
We have observed the discussions and reporting on the common use of BPA compounds that can be found in different plastics used for bottles, cookware and medical devices and is used in the manufacture of food cans and closures with some interest.
Regular press reporting of concerns about the use of BPA in baby bottle and water bottle products arose in 2008 and this led to immediate consumer reactions that quickly changed markets around the World. In a short period of time products were removed from shelves by major retailers in Canada, the US and Europe.
Consumer sentiment driven by easy access to information and greater exposure to media can move much more quickly than regulatory changes in today’s market and this has a significant impact on all the stakeholders in the market.
In less than 2 years, polycarbonate plastics have been replaced in food contact applications by existing and new “BPA FREE” materials.
The focus on BPA leaching in canned and tinned food goods is really taking off and it will be interesting to observe how the changes sweep through these markets impacting on the larger supply chain and consumers.
Our Experience
Our recent experience with BPA issues in food packaging has come through our work on Half a Teaspoon’s 321 Water Bottle product that was designed intially by Gretha Oost at Half a Teaspoon and Charlwood Design.
Traditionally, this product would have been manufactured from a polycarbonate plastic, but this is not an option in today’s market.
An alternative was required that had a unique balance of properties;
- BPA Free
- Dishwasher durability
- Functional clarity
- Processability
Eastman’s Tritan™ copolyester was chosen for the main components of the 321 Water Bottle.
In the case of the 321 Water Bottle, this was the very first instance of the Tritan™ material being processed in Australia.
Toolcraft Pty Ltd in Bayswater Victoria manufactured the tooling and moulded the components for 321 Water Bottle.
Says Darren Hind of Toolcraft, “When faced with manufacturing components in a new material we rely on the advice that can be provided by the material supplier. Eastman provided Moldflow simulations of the parts in the Tritan material. We also trialled different gate types and hot runner systems to explore what was possible to achieve with the processing and the finished product.
The Tritan material is a good material for this application and has been good to process. Much more easy to process than polycarbonates. We are very happy with what we have been able to achieve with the material.”
Tests and evaluation of the 321 Water Bottle have found that it works well in drop and impact testing, has excellent clarity and finish and reaches the feel and aesthetic vision of the design.
The 321 Water Bottle is now in production. Find out more online at www.321-water.com
In Future
Eastman’s Tritan™ material is currently priced to reflect a leading position in the market and it will not be an alternative for a wide range of polycarbonate replacement until the price of the resin falls. No doubt, other copolyester brands and other types of materials will appear in competition and prices will fall.
Takeaways
What strikes us about the situation with BPA compounds, has been the manner in which the consumer sentiment has driven a rapid change in the market that has impacted on all levels in the supply chain.
Have we reached a point where an open society will not be subjected to extended exposure to dangers due to slow changes in regulations that address health, safety and environmental concerns like have occurred in the past with asbestos use and in many other examples? We probably have.
Of course, no longer can companies wait for new regulations to drive market changes. Today’s companies and organisations need to work hard to stay tuned with their customers and end consumers – and they do. But we can always do better. Reflecting on an example serves to reinforce our understandings and confirm the importance of these activities in modern business.
Understanding customers, consumers and users needs is a vital component in producing good design outcomes and it must be remembered that these things need to regularly re-examined and researched as an ongoing part of your new product development programs.
|
|
Bisphenol A, commonly abbreviated to BPA is an organic compound that is used in the manufacture of polycarbonate plastics and in epoxy resins and other applications. BPA has long been known to be an endocrine disruptor which can mimic the body’s own hormones and may lead to negative health affects. Babies and children are at highest risk from exposure to critical levels during their early development. BPA is also thought to affect other life forms, particularly fish and aquatic life. Regulators have determined safe exposure levels for decades that are now under review.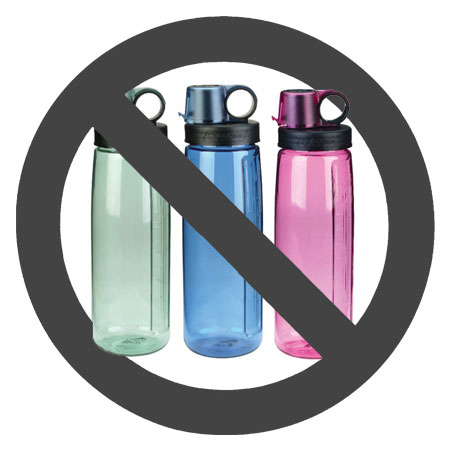
Although many countries including Canada, Denmark and France have declared their intention to ban BPA from baby and infant products since 2008, legislation is still awaiting final passage. Many countries and the World Health Organisation are actively reviewing BPA use and safe levels. BPA is now listed as a toxic chemical in many countries around the world, including Canada and the USA.
In Australia and New Zealand the Food Safety Authority does not see any health risk with bisphenol A exposure from the use of baby bottles if the manufacturer's instructions are followed. Levels of exposure are very low and do not pose a significant health risk. It has added that “the move by overseas manufacturers to stop using BPA in baby bottles is a voluntary action and not the result of a specific action by regulators.”
Eastman’s Tritan™ plastic is a newcomer to the market launched in late 2007 to specifically offer a BPA free alternative to polycarbonate. Eastman targeted Tritan™ as “a new-generation copolyester that offers a new level of flexibility and creativity for designers, brand owners and moulders of commercial and consumer housewares. Ideal for a range of moulded housewares applications, including food storage containers, plastic utensils and barware, and sports bottles, Tritan™ combines the clarity, toughness and chemical resistance of traditional copolyesters with higher heat resistance and faster processing.”
Eastman’s marketing of the Tritan™ material focuses on the consumer confidence that will flow from using the material in food contact, infant and medical products. Tritan™ is supported with a protocol of biocompatibility testing that addressing cytotoxicity, sterilisation reactions and skin irritation responses.
|