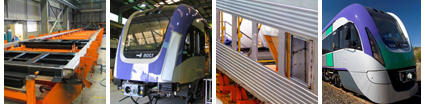
Vlocity Train
Design and manufacture of precision welding and assembly jigs
Collaboration
Bombardier Transportation is the largest train manufacturer in the world. Their manufacturing site in Dandenong Victoria has been refurbished to supply and support 38 VLOCITY trains to the Victorian Government. The VLOCITY train carriage consists of a number of main assemblies constructed from stainless steel frameworks which are assembled and welded together.
Bombardier sought assistance from Bayly for the design, manufacture and supply of the jigs and fixtures used to position and retain this framework during assembly.
Delivering outcomes on time was integral for successful progression of the VLOCITY train project. Prior to the commencement of design work, Bayly worked with Bombardier to develop the budgets and timelines for the design, manufacture and assembly stages.
Process
The design stages of the assembly fixtures were technology based. 3D CAD models of the VLOCITY train carriage were imported from bombardier’s CATIA CAD system into Bayly’s Pro Engineer CAD Tools. The required fixtures were then designed directly onto and around the existing framework.
Aiding Bombardiers visualisation of the working concept,the 3D models also enabled Bombardier to see the steps of design for each fixture and helped them to visualise the assembly procedure. This process saved Bombardier precious time in determining the handling of each item and the choice of welding equipment.
Bayly supported the VLOCITY train project over several months and provided 3D model designs, detailed design, sourced suppliers to manufacture the fixtures and managed the tooling for each assembly fixture. Bayly also managed the commissioning for each assembly fixture. This included the coordination of contract staff to assemble the fixtures and provide dimensional reports that verified the accuracy of the fixtures for Bombardier’s quality requirements.
Innovation
The key feature of Bayly’s design of the assembly fixtures included a simple, cost effective design that reduced manufacturing costs as well as reduced the overall manual labour in assembly.
The design of the jigs met the tight frame tolerances Bombardier required for the train carriages. Bombardier’s original requirement was for one welded fixture per subassembly frame.
Bayly managed to combine various fixtures into the one fixture which saved over $60,000 in manufacturing and assembly costs, as well as overall floor space in their factory.
For more details, look at our Case Study